Detecting damaged infrastructure with state-of-the-art sensors
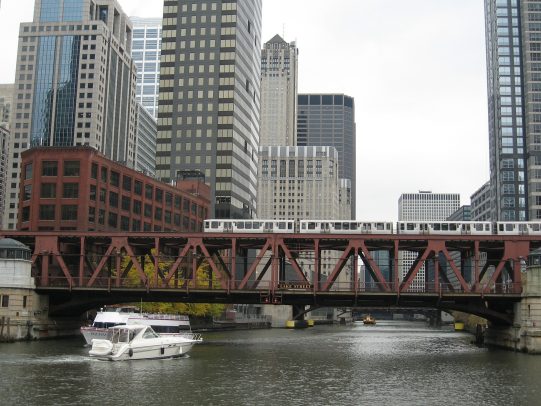
By David Staudacher
The safety of roads, bridges, pipelines, and many structures throughout the United States is questionable as they age and are pushed to perform under increasingly extreme events. The American Society of Civil Engineers gave the nation’s infrastructure a D+ grade — an indicator of the potential impact on daily life and the environment that can ripple out from failing infrastructure.
Monitoring the health of the U.S. infrastructure is critical, and among the leaders in this field is Didem Ozevin, associate professor of civil and materials engieering, who plans to incorporate micro-electromechanical systems (MEMS) sensors into the detection of damage and defects in critical infrastructure.
“The broader impact and commercial potential of this project will ensure the safe operation of critical civil infrastructures through a more reliable and cost-effective means of monitoring its health,” she said.
Ozevin plans to accomplish her goal by transitioning the MEMS acoustic emission sensor developed with her National Science Foundation CAREER research into technology.
Acoustic emission is a way of listening for cracks to identify defects before they are visible. It is well-known for detecting the initiation of damage, pinpointing its location, assessing the severity of damage and classifying the damage mode using pattern recognition tools. Unfortunately, acoustic emission sensors being used today are bulky, expensive, and significantly influenced by background noise.
“With our innovation, we will build a low-cost and low-power acoustic emission device for instrumenting infrastructures with hundreds of sensors and detecting the damage initiation at the earliest state,” she said. “Mass manufactured MEMS acoustic emission devices will take the technology to the next level by collecting big and reliable data from infrastructures.”
The MEMS acoustic emission devices will be built in an array, so that the total response is amplified by the constructive interference of carefully selected frequencies. The signal can easily be dissected into frequencies in order to understand the frequency-dependent damage modes and severity. It will block unwanted signals and distinguish artificial noise sources from active structural defects.
Once the majority of structural systems in the United States have sensors that can rapidly send information about their structural state and safety, failures can be detected and necessary precautions taken to prevent greater expenses and avoid accidents.
This project is funded by a National Science Foundation grant Ozevin recently received. Titled “PFI-TT: MEMS Acoustic Emission Device for Real-time Damage Detection in Infrastructures,” the grant is a two-year award for $249,976. The project is supported by an industrial partner, who will receive NSF I-Crops Training with Ozevin and her postdoctoral researcher.
For more information about Ozevin’s research, visit the Nondestructive Evaluation Laboratory website.